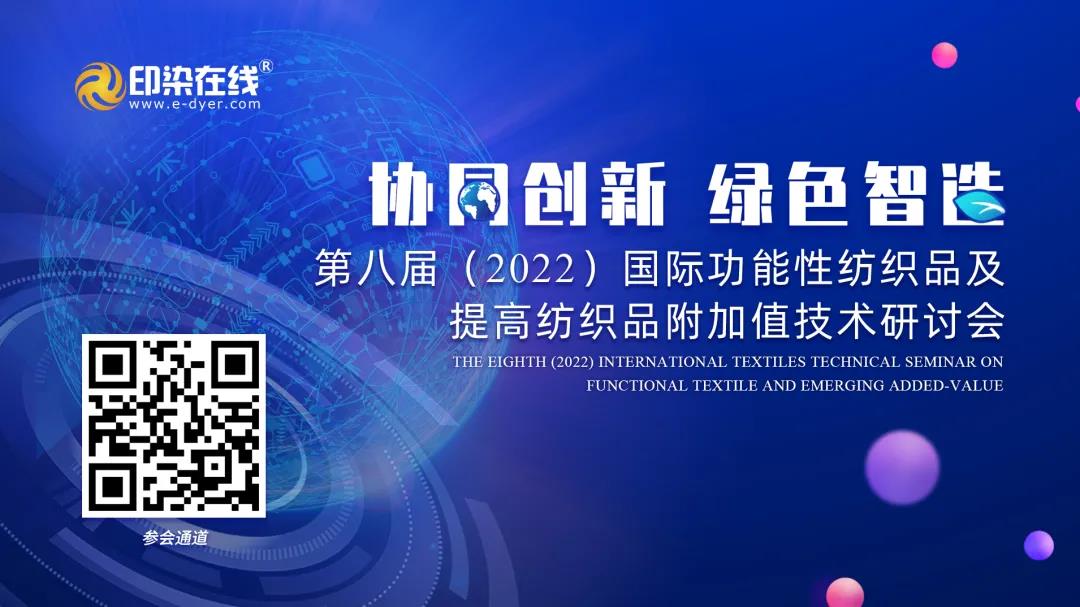
染整,是现代印染技术,是化学整理溶入印染行业之后的科学定义。包括练漂、染色、印花、整理、洗水等的总称。染整协同纺纱、机织、针织生产组合在一起,形成织物生产加工的全过程。
染整的重要性,决定纺织品质量品质的优劣,染整是产业链中带动纤维、纺纱、织造、服装及家用纺织品档次, 和附加值提升的关键技术。 染整产品,不仅反映染整的技术问题,而且集中反映了纤维原材料、纺纱、织造、染化料、助剂等多方面的综合问题。染整产品的优劣既是染厂的技术水平、生产水平、管理水平、设备水平的综合体现,也是上游坯布与纱线质量,中游染化料与助剂质量的综合体现。
练漂,是染色前烧毛、精练、漂白的总称,也是退浆、精练、漂白、丝光等加工过程的统称。练漂的目的是应用化学和物理机械作用,除去纱线和织物上的杂质、油渍、污渍,使之洁白、柔软,具有良好的毛效、均匀的渗透性。为染色、印花、后整理提供合格的前处理半制品。
练漂,属于无色处理而不被重视。实际上,染色产品质量问题60%以上源自练漂前处理。染整产品质量与多种因素相关,如坯布质量、设备状况、工艺技术、执行情况、操作状况,选用染料是否正确、染化料与助剂质量优劣等。
(1) 白度不好:主要表现在白度不够、不均匀、不纯正、污浊不透。 (2) 产生原因:一是毛坯布沾污严重、杂质油污多,织机用油质量差不能被乳化去除,漂白时除油剂用量不够。二是双氧水用量或浓度不够,工作液PH值控制不当,氧漂温度太低,分解时间不够,双氧水稳定剂用量太大或稳定剂保存时间太长失效。三是加入的烧碱或纯碱,不仅仅是提供双氧水分解所需的pH值,还是与乳化剂、精炼剂配合去除杂质的关键物质。用量不够一定会影响到白度不好,去杂不净,毛效差,不均匀,手感粗糙等。 (2)选用具有净洗、乳化、分散、渗透、反沾等综合效果好的优质精炼剂。 (3)选用优质双氧水稳定剂和螯合分散剂,控制双氧水的分解速率,吸附络合工作液中的铁及其它金属离子,防止双氧水无效的分解及铁离子可能造成的织物脆损、破洞、强力下降,失重等。 (1) 棉籽壳及杂质去除不净的主要原因是,烧碱对棉籽壳溶胀的时间、煮漂温度,碱剂用量及精炼剂用量不够。 (2) 当棉籽壳严重时,加入亚硫酸氢钠(NaHS03),有助于去除杂质和棉籽壳。 (3) 破洞及强力下降产生的原因,除了烧毛破洞、织造漏修补破洞、运输钩破的原因之外,练漂时产生的破洞主要原因是,工作液或布面带有铁离子、铜离子、镁离子等。大家知道,金属离子是双氧水的催化剂,可以促进双氧水快速、集中在布面局部分解,造成局部纤维脆损,强力下降或形成破洞。其次是织物带碱或带酸(去碱或去酸不净)存储时间过长、失水风干,出现黄斑也是造成脆损的原因。
4.助剂选用的误区
(1)一些操作人员缺乏基本的化学基础知识,不了解渗透剂、乳化剂、净洗剂、稳定剂、络合剂、螯合剂的作用。
(3)不了解哪些是阳离子型、阴离子型、还是非离子型的助剂。
(4)工人怕出现问题,错误地采取多多益善的方法,认为加入工作液中的助剂品种和用量越多越好,导致离子型助剂之间互相起反应、作用相互内耗抵消,不是作用在织物或纱线上。
(5)现场管理不严格,由于是无色处理,操作时加入助剂的量非常的随机随意,抱着无所谓的态度,不仅造成不必要的浪费,还导致表面活性剂量大,泡沫多,洗不干净残夜保留在布面上。
丝光是将纯棉、麻或其混纺、交织织物、或其纱线,浸轧在高浓度烧碱中,在常温或温度40 ℃以下张力情况下,保持一定时间,然后热水洗、水洗、酸中和获得永久光泽的产品。丝光产品尺寸稳定,对染料吸收能力增强,染色后色泽明亮、光泽持久,提高了产品附加值。
(1) 光泽不好,原因是碱浓度不够、丝光渗透剂不好或用量不够、扩幅张力不够。
(2) 丝光布纬斜,原因是坯布缝头时歪斜、进布时坯布走斜。
(3) 丝光擦伤,原因是操作不当而造成,检查设备进布撑板、导辊、针板、布铗是否有毛刺刮伤或摩擦。
(4) 折印,原因是喷淋水洗时水量不够、丝光布与撑板之间摩擦系数增大所致。
(5) 丝光布手感粗硬,原因是水洗槽残碱浓度高、水洗温度过高、带温度落布、落布时PH值偏碱性≥8以上。
(1) 严格按照工艺要求,调整丝光碱浓度、采用丝光专用渗透剂,调整扩幅撑板的尺寸和张力。
(4) 检查喷淋孔是否堵塞,保证喷淋孔的水压和水量,及时清理工作液槽中的杂物。
(1) 在生产过程中,必须经常检查水洗槽的碱浓度,防止浓碱液带入导致浓度过高。 (2) 在酸洗中和出布时,必须分批多次检查布面的PH值,应该偏弱酸性,防止存放时碱析出,形成碱斑、黄褐斑。
(1) 丝光所用的渗透剂、助剂和煮漂使用的助剂相同。
(2) 必须注意选用耐碱性能好的专用丝光用渗透剂、分散剂等助剂。
(1) 色牢度不合格,原因是选择的染料、促染剂、匀染剂、螯合剂、固色剂不合适。
(2) 色差色花,原因是所选染料组合不好、配方不合理、染色时间不够、染料与调节工作液的pH值不稳定。
(3) 跳灯和左中右色差,原因是染料发色基团配伍性不好、色相不匹配、设备运转不正常。
(4) 色点、色块、色渍和斑渍,原因是染料溶解度不好、染料颗粒偏大产生凝聚、助剂没有化好、设备不干净,沾污的焦油状物掉下、煮漂半产品毛效差而不匀、工作液含杂多、水质过硬,加入的助剂导致染料凝集、助剂泡沫太多、与染料形成包覆状有色泡沫、破灭之后形成色点、晕圈。
(5) 色泽不匀,原因是纱线条干不好、布面光洁度差、煮漂前处理杂质去除不干净、导致染色上染不匀。
(6) 染不深染不透,选择的染料力分不够、染料用量不够、前处理布面带杂质或油渍。
(1) 色牢度主要包括耐皂洗牢度、耐水洗牢度、耐干湿摩擦牢度、耐光变色牢度、耐日晒牢度、耐氯漂牢度(或耐盐素牢度)、色泣牢度、耐汗渍牢度、耐升华牢度、耐熨烫牢度以及特殊的耐海水牢度、抗紫外线牢度、耐唾液牢度等,这些牢度关键在染料结构与性能上。所以选择染料非常重要,其次才是染色工艺、技术参数及助剂的应用。
(2) 在选择染料时,必须注意染料的配伍性、溶解度、直接性、染料分子是否容易聚集、对温度和PH值的敏感性、对水质的要求等。
(3) 关注前处理布面平整度、毛效和白度的均匀度、去除杂质和去除污渍的干净程度等。
(4) 化料方法是否得当,一定要干布打湿均匀之后,先加入助剂运转均匀再加入染液。
(5) 随时检查设备的完好程度,设备绝不能“带病”工作和操作。
(6) 染色水质不佳,也是造成染料与金属离子结合或与杂质凝聚导致色花、色浅、色不匀、色不符、重现性不好的重要问题,因此保证水资源是染色成功的关键。
(1) 目前染色的助染剂很多,染色是所有染厂最重视的工序。然而,越重视恰恰也是最容易出问题的地方,在染色过程中并非加入的助剂和品种越多越好。
(2) 有的企业只相信常用的JFC渗透剂,作为万能助剂应用到所有的产品上,没有考虑到JFC的浊点(浑浊点)只有38-42℃,超过43℃其渗透力就会失去作用而造成质量问题。
(3) 习惯性地一只匀染剂用到所有的棉、毛、麻、丝、化纤上,殊不知所有的纤维性能是不一样的,适合的匀染剂也不一样。
(4) 皱条和起毛产生的主要原因是设备问题,装布量大、浴比过小或操作问题。装布量太大时,容易造成布与布之间的压力、张力和摩擦力加大,泵压与泵提升织物的难度加大,影响到布面的平整度而产生皱条和布面起毛。
(5) 风印与助剂的关系不大,关键是染料本身的耐酸耐碱性,半制品织物自带的酸碱性,车间空气湿度和酸气等有关。例如活性翠兰KN-G、艳橙X-GN对酸碱敏感容易产生风印,分散黄RGFL对碱敏感也容易产生风印。
(6) 染料选择必须考虑到分散和助溶的双重作用、渗透作用及对水中金属离子的络合作用、对pH值的适应性、泡沫性等对上染率有影响的多方面因素。
(7) 必须强调的是正常干摩擦牢度好于湿摩擦牢度,当我们遇到湿摩擦牢度达标,干摩擦牢度不合格时,必须优先检查烘干、高温定形时温度是否太高,可以肯定地说是部分染料升华或高温染料分子被破坏所致。尤其分散染料在高温条件下染料升华,导致干摩擦牢度低,彩条色织面料之间搭色等很常见的问题 (1) 有的染整厂担心色花,不考虑相似相容性而将渗透剂、匀染剂、螯合分散剂、防止色花剂、PH值控制剂、润滑防皱剂、浴中柔软剂、浴中宝等统统加入到工作液中,导致各种助剂之间的“相互厮杀”起反应,内耗作用和功能性。
(2) 匀染剂对改善色花、色点的确效果很好。但是应该知道的是,它也是一种缓染剂,在起到匀染的同时也具有移染和阻止染料上染的作用,加入量少达不到匀染效果,加入量多了抢占染料上染的染座,反而染不深得色浅。
(3) 扩散剂N是常用的分散剂,然而它在高温下其抗染料凝聚作用大大降低。
(4) 当选用的非离子表面活性剂不合适时,导致在浊点以上非离子表活剂自身析出或分解、吸附染料而成焦油状物质粘在织物或设备上,造成质量问题。
(5) 螯合分散剂的质量也会影响到匀染问题,水质好的企业不一定加入螯合剂。
(6) 工作液的pH值往往不被重视,染色时没有实测与监控。代用酸代用碱的出现是为了提供一种像缓冲液一样,保持稳定的pH值,更好的助染。事实上,由于没有统一的产品标准,目前市场极为混乱。建议当不知道成分时,还不如直接用适合的冰醋酸或者有机酸,绝不能使用硫酸H2S04和盐酸HCI类无机强酸的代用酸。
染色后的各种整理是赋予产品特种功能、提高产品附加值的重要手段。目前,主要分为物理机械整理和化学功能整理。机械整理包括拉毛、磨毛、剪毛、梳毛、烫毛、摇粒、预缩整理和超柔机械整理等。化学功能整理种类繁多,分为常规的柔软整理、增白整理和特殊的功能整理。下面主要以化学整理为例分析。
(1)柔软效果达不到要求,原因是柔软剂质量不好、柔软剂选择不合适、用量不当、处理温度和时间不当、定形机参数设定不当。
(2)柔软斑,原因是柔软剂质量问题、软片化得不好或没有过滤、布水洗不干净有残留物化学物质、柔软剂破乳漂油、柔软剂入缸的速度太快。
(3)色变,原因是柔软剂品种不适合、柔软剂离子性太强、布面呈碱性所致。
(4)色牢度下降,原因是柔软剂品种不合适、柔软溶液偏酸性太强、工艺参数不合适。
(5)色花,原因是柔软剂对染料有萃取、剥色、拔色作用,pH值选择得不合适。
(1) 筛选质量好柔软剂,不同柔软剂的柔软度、蓬松度、平滑度、油滑度、柔糯度是不一样,直接影响着织物的亲水性、吸水性、拒水性。
(2) 化好的柔软液稀释过滤才能使用,在硅油软片系列中,具有多种改性基团的硅油软片,如羟基硅油、氨基硅油、环氧改性硅油、羧基改性硅油等,选择匹配使用。
(3) 柔软色变泛黄,是氨基硅油软片中的氨基所致,阳离子软片虽然手感好,易吸附在织物上,缺点就是易泛黄、亲水性差,应选择使用。
(4) 影响色牢度和色花的柔软剂必须更换掉,柔软前的织物和设备必须清洗干净。
(1) 尽可能不在染缸内做柔软处理,染缸内经常在酸碱和染料之间变化,带有清洗不净的酸碱或长期使用设备上的污垢掉下来影响柔软效果。
(2) 防止柔软剂漂油挂在缸内,严重时将影响下一缸布的染色效果。
(4) 硅油柔软剂对水的硬度很敏感,硬度大于150mg/L时水中极易破乳漂油。
(2) 配好的柔软工作液随意加HAc冰醋酸,应该测试好PH在6-7为宜。
(3) 柔软整理看着简单,实际对面料手感的影响很大。
习惯上是棉织物的防缩防皱防油的三防整理,多用在机织物上,针织物上主要进行防缩防油整理。这类三防整理的织物曾经在上世纪广为流行,现在主要用于特殊的工装服。新的三防整理主要是防水、透气、透湿的户外运动面料整理。关键是选好三防整理剂的同时,通过高支高密、紧度大而密实的异形纤维,多层结构的织造技术相结合,才能生产好的新三防高档面料。
主要包括抗静电整理、阻燃整理、抗菌消臭整理、防紫外线整理、拒水拒油整理、防水透湿整理、防寒保暖整理、吸湿排汗整理、远红外负离子整理、仿真丝丝鸣整理、抗菌防霉整理、防螨防蚊虫整理、药物及磁性整理、核生化防护整理、防弹衣整理等等。
检查设备拉毛、磨毛辊或针布是否有破损,布面与拉毛辊之间的距离和设定的工艺参数是否合适,选择适合的起毛油、拉磨毛的专用助剂。
设备要经常检查,包覆的针布不能出现倒针、歪歪斜斜,砂带不可出现破损等。
是机织物尤其是亚麻织物广泛使用的技术,自50年代初,前苏联援建的我国第一个亚麻厂(哈尔滨亚麻厂)开始一直使用的技术。目的,使麻皮、麻草、木质素、果胶质等杂质充分溶胀,通过低浓度硫酸酸洗之后磺化,亚氯酸钠漂白溶解,双氧水复漂达到80以上的白度。该技术占地面积大、工艺流程长、冷堆时容易产生碱斑、黄褐斑、霉变以及水的自重沉淀导致上下层毛效不均匀,亚氯酸钠漂白腐蚀性和污染性强,在九十年代全国崛起的新建亚麻厂已经不用该项技术。但是在强调节能减排的今天,设备采用退浆、煮漂联合机组中漂白部分的浸轧-折叠式冷堆,汽蒸,连续式喷淋与双脉冲式水洗,以及配合多种新助剂的出现,再次被染整厂使用。对于间歇式冷轧堆后,必须进入染缸再加热到80-95℃使双氧水充分分解,氧化漂白、除氧、中和、水洗等,与常规的95-105℃直接快速煮漂的优缺点,各有其长短,有待商榷。
机织物退煮漂联合技术自六十年代起,已经使用多年。在针织面料上的应用是近几年开始起步的,无论设备在无张力创新、自动化程度提高、智能化操作方面,还是在配套助剂的开发应用方面都得到了长足的发展,使用的企业也越来越多。连续式平幅煮漂生产线与间歇式染缸比,减少了织物加工过程中的褶皱、拉伤、摩擦、起毛等问题。但是经向张力即使采取主动传动,消除部分张力,针织物的集圈组织结构还是会变形。因品种而异,合理搭配使用。
针织面料适合小批量、多品种,变化快是一直以来的优势。在煮漂时,浴比太小容易造成织物擦伤、杂质去除不净,影响到织物的白度、毛效及均匀性。建议浴比控制在1:5-8属于正常合理工艺,再配合优质的煮漂助剂是值得推广的工艺技术。
是先将染料包裹在微胶囊里之后,对纺织材料进行染色的一项新技术。染色时先将微胶囊里的染料,通过抽真空溶解在纤维材料重量的5%-20%的水中[传统工艺纤维材料:用水量(浴比)1:5-12],再对纤维进行染色。 该技术特点是大大节约水资源,技术关键在于微胶囊的制作和抽真空溶解技术。微胶囊制作所用的材料是热塑性的脲醛树脂、石蜡基质、酵母细菌、烯偏聚氯乙烯、聚烯烃、聚酯、聚氨酯、聚氨基聚酯、聚丙烯酸酯、聚醋酸乙烯酯、聚苯乙烯及其共聚物、聚脲酯等。微胶囊粒径在5um-300nm的范围。该项技术属于前沿技术,还处于试验开发阶段。
早在上世纪70年代末,德国特恩机械公司(THEN)率先提出气流雾化染色的概念,并最先提出用气流代替液流输送织物的气流雾化喷射染色机( THENAIRFLOW)。同期,还出现高速喷气织机和喷水织机。 原理都是采用空气动力学理论,将高压鼓风机产生的高速气流(或水流)注入喷嘴:另一管路向喷嘴注入染液,染液与高速气流在喷嘴中相遇并混合形成雾状细微液滴后喷向织物,在喷出的压力下带动织物运行,使得染液与织物在很短的时间内充分的多次接触,达到均匀染色的目的。 目前,该项技术被广泛应用到生产气雾染机的设备中。由于气雾染色用水量极少,污水染排放少,更适合吸水率、含水率低的合成纤维织物染色。对于吸水和含水率高的棉、麻、毛织物不是十分适用。
xx公司和xx公司展出了气液式染机和展幅式气流染机。xx公司是采用风带动织物循环运动,用水量少,只要将织物浸湿再加200L的循环用水就可以实现染色。 浴比低至1:2,织物呈现开幅状态运行,染液容易均匀地喷洒在织物上,不易染花,经向拉力小不会产生经向褶痕,弹性纤维织物不会卷成绳状,适合各种织物染色。xx公司的气流染色机是开放式弧状喷嘴,气液混合后喷压织物,渗透性强,具有温度均匀、压力稳定、颜色重现性高的特点。适合于机织物、针织物、高密度超细纤维与弹力织物、强捻织物等多种织物染色,浴比1:4以下。
超临界CO2染色技术(又称为无水染色)研究已久,是大连卓尔高科技有限公司承担的超临界流体国家85科技攻关项目。 超临界二氧化碳染色流体技术,作为一种新型清洁的染色方法具有上染率高、染色流程短、无污染等特点。原理是,根据超临界CO2对有机物的溶解性随溶质极性、分子量、密度的不同而不同。容易溶解非极性或极性小,分子量小的有机物。而多数分散染料分子极性弱、分子量也不大是无水染色研究的主要对象。 二氧化碳C02在超临界状态下形成的流体粘度低,分散染料在超临界流体中杂乱分散的状态下,染料分子非常活泼,能够快速达到纤维表面而容易渗透到纤维内部上染。分散染料在流体中分散性高,溶解度随着流体的密度增加而增加,用压力和温度控制C02的密度来控制染料的溶解度,控制染料的上染率。 由于超临界CO2流体完全代替水作为染色介质还有很长的路,所需要的超高压设备就是阻碍其广泛应用的最大障碍。但是,超临界C02流体可以在常温下,通过调节离子流体的疏水组成进行染色,涉及到专用设备、纤维改性、染料组合、助剂匹配等多方面的联合研究、协同攻关之后,才可能实际应用。 泡沫处理织物的设想,最早可追溯到1931年。1971年瑞士Sandoz公司研制成Sancoward工艺,但均未受到应有的重视。1973年之后出现了席卷世界的能源危机,在能耗费翻倍甚至更高的形势下,促使国内外的专家学者对泡沫染整技术进行了大力的研究和攻关。上世纪八十年代中期,我国曾对泡沫染整技术的开发和推广应用达到了高潮。在九十年代后,泡沫染整的研究应用逐渐趋于缓慢。主要原因:一是由于当时技术水平限制;二是当时人们的“环保”意识淡薄,各生产企业没有采取强有力的环保制约措施。时至今日,强制性节能减排、绿色环保成为国策的时候,泡沫技术再次引起人们的重视。
泡沫染色,是在染液中加入发泡剂,将染液加工成泡沫的形态后再施加到织物上去。与常规技术相比技术特点是:具有精确给液、无头尾色差、染液喷入深度可控,可以实现单面染色,节约生产用水和热能,提高车速等优点。具体方法是,在含有表面活性剂(发泡剂)的染整加工液中通入空气,以机械旋转剪切的方式形成泡沫,通过泡沫施加器把这些泡沫均匀地施加到织物上进行泡沫染整加工。泡沫染色存在的问题是,发泡的稳定性、施加的均匀性、泡沫大小、破灭到消失时间等都影响着染色的质量,有待于完善之后才能推广应用。 泡沫整理,应用领域已经非常广泛,包括:柔软泡沫整理、防水泡沫整理、阻燃泡沫整理、抗菌泡沫整理、易去污泡沫整理等。机织物免烫树脂整理烘干时,产生泳移现象是棉织物传统整理中遇到的最为严重问题。泡沫整理带液率低,泳移程度也会相对降低。因此,将空气做化学品的媒介,使化学品在织物上均匀分布,大大减少甚至消除了泳移现象。另外,折皱回复角、耐磨性、拉伸强度、撕裂强度和抗弯曲磨损性能都得到改善。在洗涤过程中,织物幅宽收缩减少,织物手感和洗可穿性都得到提高。因为,带液量大大降低,在达到与浸轧同等效果的情况下,可节省大量能源和水资源而值得推广。 是建立在更加安全完善的生产加工链上,进行纤维材料、染料和使用的化学品必须是环境友好的,对人体和环境不产生有害影响的染色技术。它的生产加工过程是安全、生态,不会破坏资源环境和污染环境。由于生态染色无论对染料、助剂、工艺、生产过程的控制都非常严格,鉴于染料的稀缺性,面料价格偏高。相信随着越来越多的消费者开始关注生态化,购买生态内衣、生态童装、生态家纺、生态玩具等将成为生态染色的突破口。
生物酶技术在纺织上已经得到广泛应用,从麻的生物酶脱胶、棉织物生物酶退浆、精炼、除氧,染色后仿旧的生物酶洗、生物酶柔软整理、生物酶酵素去毛整理,到印染废水的生物酶处理等等很多不再赘述。
纺织品的物理机械染整加工技术,是随着科技创新、行业互相渗透而兴起的高新技术。超声波技术、高能电磁波辐射技术、低温等离子体技术在染整加工中已经逐步应用。例如:纺织品风格方面的机械柔软,绒面、纹面、皱面等物理机械整理,人造毛皮特种织物的物理机械纹理加工,以及毛织物的干、湿整理等等。
功能整理是提高产品附加值,提高企业经济效益最显著的工艺技术。包括:抗皱整理、防缩整理、防水防油防污三防整理、易去污整理、吸湿排汗整理、阻燃整理、抗菌防臭整理、防霉防蛀整理、防紫外线整理、防辐射整理、香味整理、陶瓷(保健)整理、保暖透气整理、防水透湿整理、发热保健负离子整理、仿真丝的丝鸣整理、免烫整理、防螨防蚊整理,及特殊行业的医疗保健整理、磁性材料整理、医用纺织品整理、电磁波屏蔽整理、核生化防护整理等等。 在这些整理中,共性都是纤维自身没有的功能,通过人为干涉赋予和人们需要想象的功能性整理。
(2)如何按照人们设计的效果,通过粘合、反应、络合等多种方式附加到织物上,并且保证一定的耐洗次数。
(3)功能整理效果评价、测试方法。因此说,功能整理剂和不含有害化学物质助剂的研发,是目前染整企业、助剂企业提高产品附加值,以及创新与发展、设计与研发的最大空间,最有研究和开发价值的部分。
新材料开发新织物中的问题 随着科技的迅速发展,新纤维、新材料,特别是多种复合纺织新纤维新材料在纺织面料方面的开发将越来越多。新纱线、新织物组织结构将打破常规愈来愈复杂,人们要求的自身性能、附加的功能性会越来越新、越来越多,导致染色工艺、染色技术随之也越来越难,不可控因素加大。
目前,有一些染厂由于技术力量薄弱,民企老板只让技术人员在企业干活,很少参加技术交流会寻找学习的机会,每天只盯在每一缸布出来是不是合格、是否花掉方面,对于新纤维新材料开发的新面料,新型助剂一无所知,一直沿用传统工艺不做研究与改进,严重地影响了新产品的价值和服用效果。
在采用新纤维、新材料开发新产品方面,无论是纺纱、织造、染整人员,还是染化料助剂厂的技术人员,都必须了解一些纤维材料的基本理论知识。根据其微观结构性能制定设计合理的产品,有的放矢地研究新产品开发的技巧十分重要。尤其染整工艺的制定,染化料的选择,一定要结合纤维高分子结构的主要材料选择染化料助剂。根据它的分子链段链节、玻璃化温度、熔融温度,制定染色工艺和定形工艺。 目前,有一些品牌公司和研发能力强的企业,为了防止同业人员仿造、抄袭,延长新产品的生命周期。从纤维选择、纺织用的纱线到面料开发,纤维种类多达5-8种之多,还要求产品达到同色性好,毫无疑问给染整厂带来很大的技术难度。 建议,无论千变万化多种新纤维的出现,一个宗旨是抓住纤维的主要成分,根据纱线或面料的主体纤维选择染料,制定工艺技术流程,然后兼顾到耐化学性能、耐温度较弱的纤维,制定工艺参数、选择化学助剂,必须优先打样,筛选、优化制定合理的工艺技术方案,放样调整之后再逐步推广生产。
染厂生产离不开新面料、染料和化工助剂,纤维厂离不开纺纱厂和织造厂。随着新纤维、新染料、新助剂的不断出现,技术发展和科技进步,从纤维原料开始协同作战,解决染整前处理和染色,印花和功能整理问题,提高产品附加值才是共赢、互赢的关键。发展方向是学科交叉、技术渗透、相互服务、公开竞争就是企业生存与发展的方向。
来源 :印染厂、TEXHR纺织人才网